|
|
|
Compression Molding
Compression, the most basic type of
molding, starts when the mold is removed
from the press and opened. A pre-cut or
shaped piece of uncured rubber of
pre-determined weight is placed into the
cavity. The metal insert to which it is
being bonded is also placed into the
cavity at this time. The loaded mold is
placed back into the press and the press
is then closed. The pressure forces the
plates together causing the uncured
rubber to flow into the shape of the
cavity in the mold. A slight excess of
material flows out of the cavity along
the gates and vents allowing the mold to
close. The semi-positive design (the
extension of the top plate into the
cavity) is used with some parts that
require a ram-like additional push on
the material during the final closing of
the plates. The mold remains closed
until the rubber is cured, completing
the cycle.
Compression molds do not consume
additional rubber when filling the
cavity like the “runner” of an injection
mold or the “pot” of a transfer mold.
While being conservative in the amount
of rubber used to make the part, it
requires a greater amount of effort to
weigh and prepare each individual piece
of rubber. Compression molds take longer
to cure and each piece of rubber is
hand-loaded into the cavity. Due to the
simplicity of the mold, however, this is
the most economical way to mold rubber
parts.
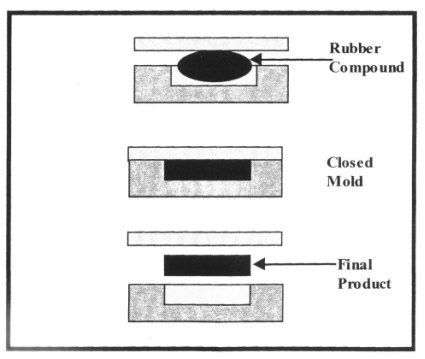
CUSTOMER TESTIMONIALS
|
|